Achieving the quality standards that allow the Santa Maria brand to create award-winning spices is about more than securing the best ingredients. What happens to them when they reach the factory is equally important. Discover how factory processes support the brand’s sustainability ambitions while enhancing a superior taste experience.
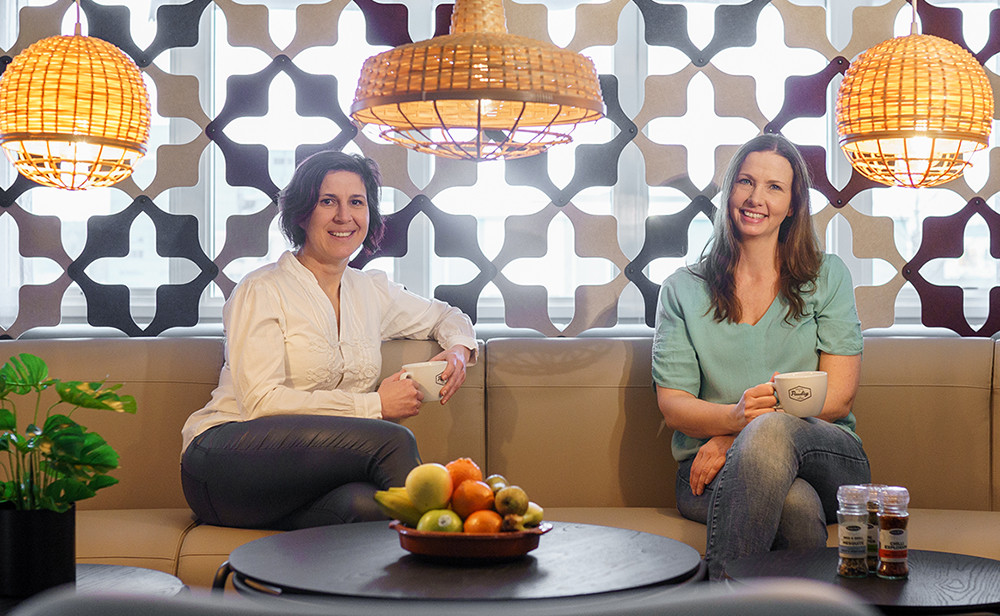
Photo: Agnes Wärnegård, Quality Assurance Manager, and Anna Sjööquist, Factory Manager
Welcome to Mölndal, Sweden, where one of Paulig’s two spice factories is located! Here, 80 dedicated employees are keeping busy curating Santa Maria’s popular spices and spice mixes.
Santa Maria spices are renowned for their outstanding taste and quality, which has earned several of them the prestigious Superior Taste Award. While this is testament to the high standards and skills of growers and suppliers, how Paulig handles the raw spices during production also has a profound effect on flavour.
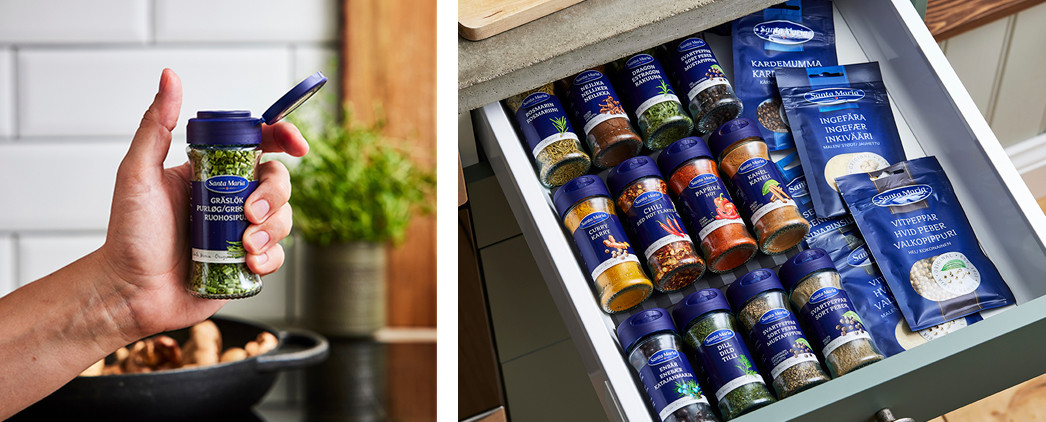
Agnes Wärnegård, Quality Assurance Manager at Paulig’s Mölndal factory, explains:
- Cleaning and sorting the raw spices is crucial. Our oregano is a great example of this. Although it’s already been sorted before it reaches us, we’re extremely particular with how we treat oregano. So, in another cleaning process here in the factory, we remove around a further 30% of the raw spice in order to achieve the purity standards we’ve set.
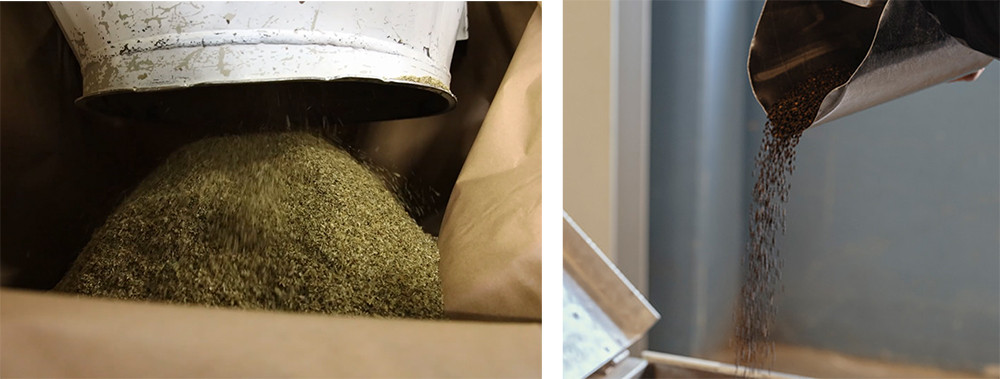
Agnes Wärnegård continues:
- Our pepper is another case in point. We purchase whole peppercorns which are then carefully ground into different sizes in our factory. This size variation releases more complex taste characteristics adding further dimensions of flavour to the finished product.
Quality control in focus
At Paulig’s factory in Mölndal, Sweden, an onsite laboratory is also a crucial part of quality control. Among many tasks undertaken in this lab, two dedicated staff continuously test flow characteristics of ground spices, carry out taste testing and conduct microbiological analysis.
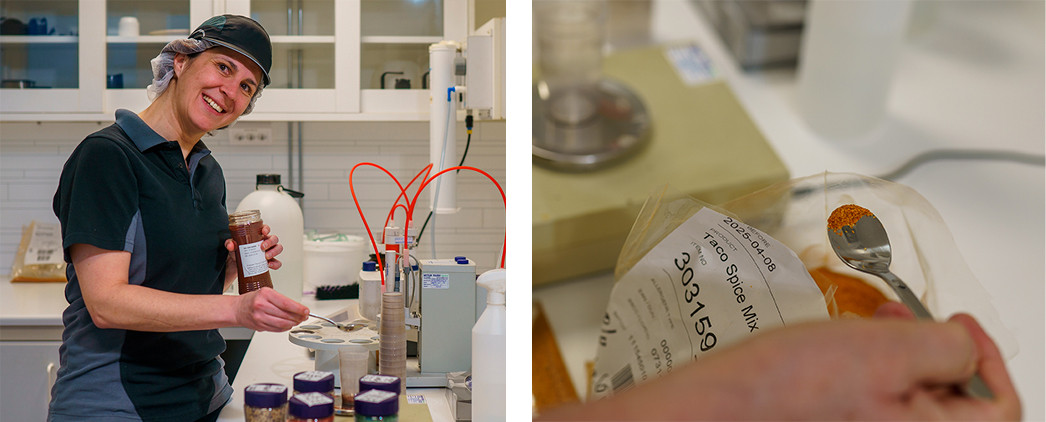
Photo: Agnes Wärnegård
- At our factories, we’re committed to continuous process innovation. Together with production line monitoring and product checks every 20 minutes to ensure quality and check packaging integrity, our lab is an important part of this, says Agnes Wärnegård.
Innovating with waste products
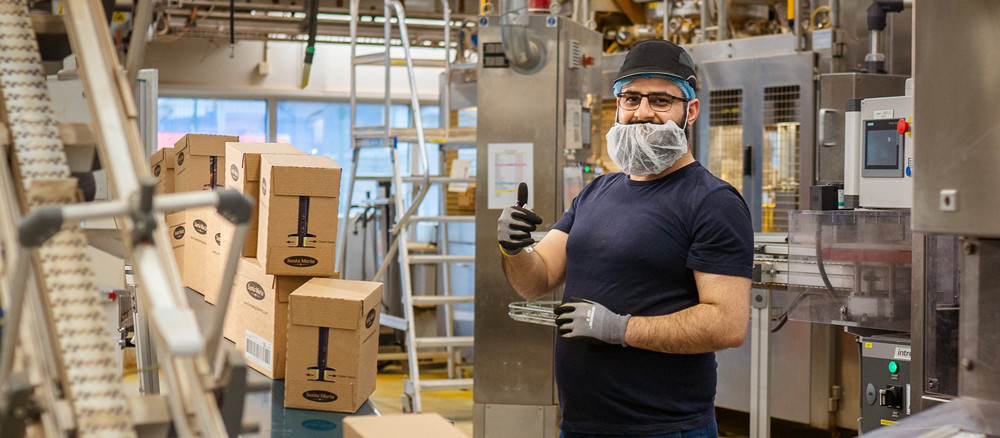
Photo: Rawand Mohammed, Machine Operator
In any production facility, waste and how to deal with it is a challenge. Paulig is constantly looking for ways to reduce waste in processes. For example, at the company’s factories, salt is used for cleaning purposes and previously, after it had been used, it was simply sent to landfill. This no longer happens as this salt is now recycled and re-used in soil treatment. The result is that over 300 tonnes of waste material has been given a new purpose.
Climate impact on the agenda
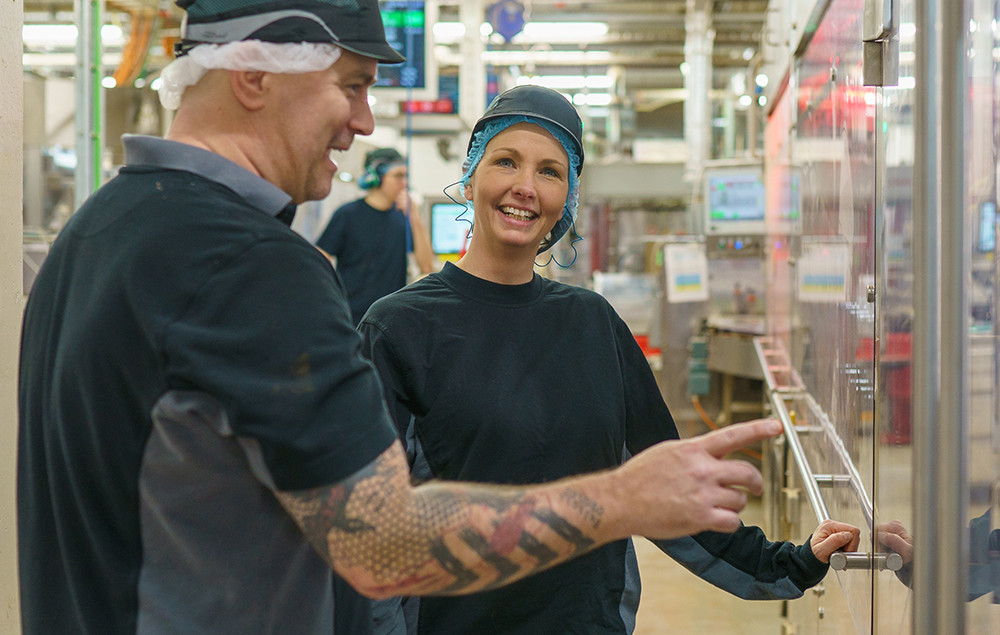
Photo: Henrik Rosenquist, Technical Engineering & Facility Manager, Anna Sjööquist, Factory Manager
Paulig’s Mölndal factory is certified as CarbonNeutral® building. There are many factors behind this, but as Factory Manager Anna Sjööquist explains, energy has a profound impact on Paulig’s sustainability ambitions:
- As you can imagine, our production processes demand significant amounts of energy. To minimize their impact, we have invested in energy efficiency and heat recovery and switched to buying biogas, renewable electricity and district heating.
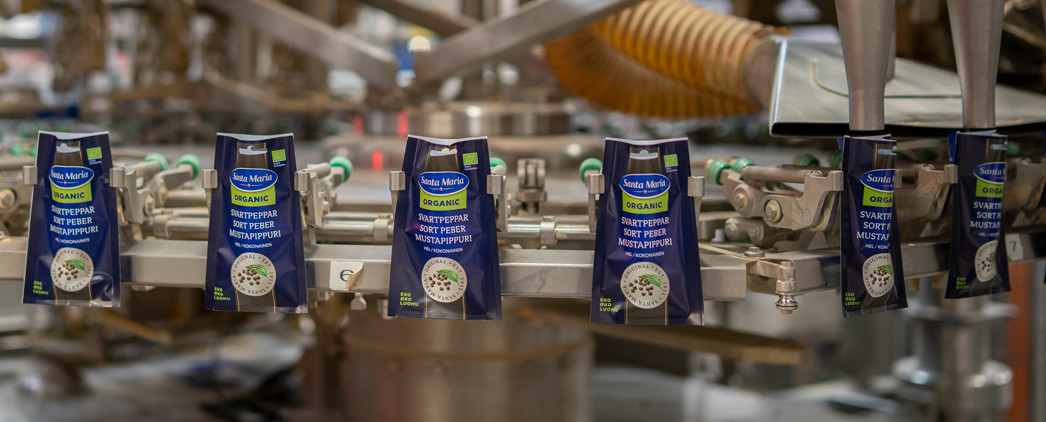
Staying on this subject, Anna Sjööquist also highlights an important logistical change which will have a significant effect going forward:
- To transport ready products from the factory to our warehouse facility here in Gothenburg, we’re about to make the transition from traditional trucks to electric. Considering that 5 transports per day make this return journey, the impact this change will have on our energy consumption and CO2 footprint will be significant.
Read more
- Santa Maria spices receive Superior Taste Awards for exceptional taste
- Visiting the home of Santa Maria’s award-winning cardamom
- A journey to the mountains of Peru - bringing home the best oregano in the world
- From the red soils of Kerala comes the King of Spices
- Paprika at its finest - a visit to Paulig's supplier in Spain
- True or false cinnamon - a myth explained
Top photo: Dena Akbar, Machine Operator